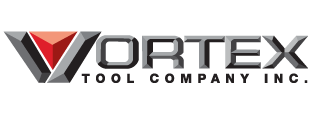
Upcut Spirals
- The upcut spiral is a right-hand spiral with a right-hand rotation of cut. An upcut spiral will cause the chips to be “augered” upwards during cutting.
This can be particularly useful in slotting cuts or where chip removal is a problem. Upcut spiral bits have a tendency to “lift” the part in some cases. Additional holding power or stepped cutting may be required. - Upcut spiral bits will leave a smooth cut on the bottom of a thru cut and tend to leave some fuzzing on the top edge in certain materials.
- Upcut spirals straight plunge/drill and have good end cutting geometry.
Downcut Spirals
- A downcut spiral (right-hand cut, left-hand spiral) causes the chip flow to
be directed downward. It also helps hold down the part being cut. The
edge quality on the part is smooth on the top, but tends to be fuzzy on the
bottom in certain materials. - The downward chip flow can sometimes cause clogging problems particularly in a blind slotting situation.
Downcut bits tend to preload the routing system and can substantially improve part hold down in a
marginal routing setup. - Downcut tools CANNOT be used to plunge straight into wood and should be ramped into the part.
Compression Spirals
- A compression spiral is designed with both upcut and downcut flutes. The
upcut and downcut flutes compress the material being cut, preventing
chipping or fuzzing on the top and bottom of the cut. - Compression spirals are used extensively for cutting double-sided laminates, and can be used on natural
woods where edge fuzzing is a problem.
The information given should only be used as a guideline or starting point for feed rate selection. Your
actual feeds and speeds will vary widely as a result of “contributing factors” such as machine rigidity,
horsepower, collet condition, spindle integrity, part clamping, hold down, and many other factors. Generally
speaking, solid carbide tooling will perform better (i.e., longer life, less tool breakage) at faster feed rates. We
recommend a “starting point” feed rate and increasing that feed rate until part finish becomes undesirable or
other limiting factors become evident.
NEED HELP FINDING THE RIGHT TOOL?
Vortex Tool has created a video to help guide you through
our Composites and Aluminum Tooling Selection.
Scan the QR Code or visit https://www.vortextool.com/composites-aluminum-tooling.html to view the video.
FREE QUOTE
Do you need Assistance with this product? Fill out this form to get in touch.
OFFICE LINE
1.800.555.6789
EMERGENCY
1.800.555.0000
WORKING HOURS